"It's an affordable archiving solution that
integrates easily with our existing business
applications."
That's Boyd Corporation I.T. Manager
Steve Prices's
take on what the key factors are that make their
deployment of the UnForm document management software a
success.
Affordability made acquisition of the software easy
and painless. Integration capability with the company's
custom-developed Progress 4GL-based ERP applications
meant both a comfort level with the development
environment, and a leveraging of previous I.T.
investments.
"To us that meant very low risk, with
potentially high returns. Something we could put on the
fast- track."
Background
For a number of years the growth of the number of
files stored on different network servers at Boyd's various regional locations had been a
nagging problem for Steve. There were
inefficiencies both in storing and accessing
files, as well as in the administration of the
underlying file systems.
Considering the Boyd business model and after
research into available technologies and solutions, it
became obvious there was a strong argument to be made
for a more centralized approach to document storage and
retrieval.
After considering the acquisition of an
electronic archiving solution from one of the
traditional leaders
in the DM solutions marketplace, Steve realized that the
approval process itself could take years, considering
the large price tag involved.
So in 2006 he was pleased to discover that SDSI, the
developer of Boyd's existing UnForm laser forms software, was
offering a much more affordable document management solution. This
would break down a key barrier to acquisition, namely,
it eliminated the need for higher-level approval since
the price tag for the UnForm DM solution was well inside
the budget authority of his department.
And the UnForm technology itself was
client-server based, which meant
direct integration of archiving and document management
capabilities with Boyd's ERP applications.
UnForm
also included another benefit no other solution could
provide: the capability of archiving PDF's from the ERP
print streams without scanning. Other solutions would
have required significantly more scanning, which is
considerably
less efficient than capturing documents at their source
creation point, when practical.
The savings and efficiency gains so far have been
significant.
Steve described to us some of the
early archiving projects undertaken and their impact:
Centralized AR Invoicing
One of the first document archiving projects
implemented has eliminated 1500 hours per year of
clerical labor for an annual savings of $30,000, by centralizing AR invoicing at the
company's headquarters. This had not been feasible until
a central electronic document repository for
invoicing-related documents was in place.
The system works like this:
Order pick
ticket and manufacturing routers are now bar-coded and archived at the same time that they are
printed by UnForm. Upon factory completion of the order, the printed versions
of the order picking list and manufacturing routers are
scanned and uploaded using UnForm's image manager tool,
so that all related factory notes and markings are
captured, as well as any auxiliary documents that need
to be retained. The bar-codes on the picking list and
router documents allow for an automated capture of the
archive index properties that match the documents
together in the archive for quick retrieval. The scanned images are
stored as multi-page PDF files with the original archive
copies of the order and production router. The entire
packet of information is then available electronically
to the central invoicing clerk, as well as other
authorized users.
Immediate access to the scanned packet of documents is what
allows invoicing to be centralized, since the invoicing
process relies on information contained on the documents
that come out of the factory.
-
Custom centralized invoicing application
developed in Boyd's Progress 4GL Web-Speed
environment.
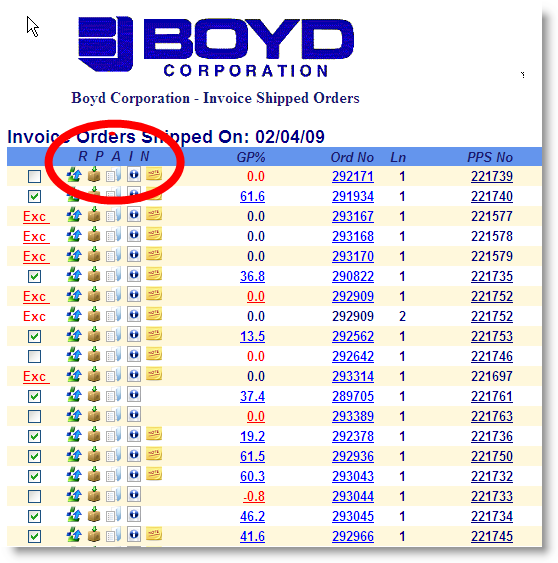
-
Close-up of the Archiving link column
which gives the invoicing staff access to the
centralized archive documents. The link uses the
UnForm client API behind the scenes to retrieve and
display documents needed to finalize invoicing.
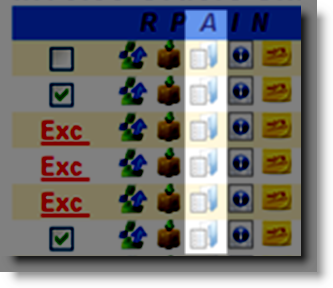
Quoting/Estimating
Another Boyd project using UnForm
archiving made a direct impact on the
efficiency of customer service operations:
Boyd is a custom fabricated products manufacturer.
Their
operations hinge on the ability to estimate and quote
jobs accurately based on customer-provided
specifications that are submitted to Boyd in electronic PDF and
CAD files.
These files are initially collected by
Boyd customer service
representatives. Boyd estimators then need access to
these files to prepare quotes. The easier the access to
these files, the more efficient the process and the
higher the volume of quotes that can be processed
without adding staff.
The Progress 4GL software Boyd uses has a web development environment
called WebSpeed, which lets them develop web-based
applications that integrate with the main Boyd ERP
system. Boyd I.T.
staff added web hotlink buttons to the quoting and
estimating web application screens to allow browsing for
and uploading customer documents
to the UnForm archive, and to retrieve customer documents from
the UnForm archive. These processes use UnForm's client
API for an integration that is entirely transparent to
the users.
The central electronic repository that now exists for
these documents, and the access to the documents via a
customized internet web application, have improved the
efficiency and coordination of the various departments
involved, resulting in a significantly higher
departmental capacity for prospective orders.